Thermal bridging in a residential build - A case study
PERINSUL HL
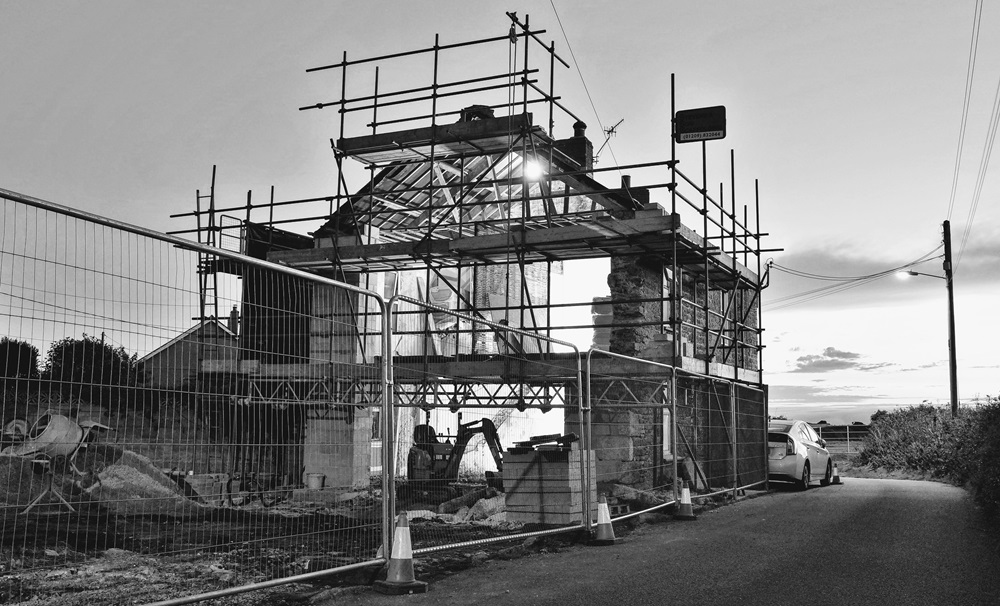
Addressing thermal bridging in building design and construction is not just a question of excess heat loss, energy use and carbon dioxide emissions. It is also about the health and comfort of the people who use a building, whatever its shape and size.
A PERINSUL case study.
Statement public buildings and commercial developments often take the limelight when it comes to claiming better energy efficiency, environmental impact or wellbeing. Thermal bridging solutions in domestic construction, however, have the potential to be employed in many thousands of new and existing homes - and therefore to make an even more significant collective impact.
How can traditional buildings
be future proofed?
When it came to altering and extending an old miner’s cottage in St Just, Cornwall, taking a best practice approach to thermal bridging was one of a number of measures designed to “future proof” the traditional construction.
Nick Donaldson, of Nick Donaldson Architect, took on the roles of client, architect and builder so that he could turn the cottage into a home capable of adapting to his family’s changing needs for decades to come. He modelled the proposed design for the Passivhaus standard, adopting low-energy building techniques throughout.
“The house is in poor condition, damp, cold (poorly insulated), leaky and in need of extensive renovation,” wrote Nick as part of the planning application to his local council.
As a member of the Association for Environment Conscious Building (AECB), Nick was also keen to ensure that the project achieved broader environmental aims, like the use of materials with a lower environmental impact (such as cellulose insulation - recycled newspaper - in the walls of the extension).
What is the Passivhaus standard?
Developed by the Passivhaus Institute in Germany, the Passivhaus (also written as Passive House) standard is a low-energy building standard that aims to achieve a defined level of energy consumption, as well as a minimum level of comfort for occupants. Despite its name, any type of building can achieve Passivhaus - but the concept was first demonstrated in domestic projects.
The Passivhaus standard applies to new construction, while the counterpart EnerPHit standard is used for retrofit projects. The performance thresholds for EnerPHit are relaxed slightly compared to Passivhaus, in recognition of the difficulties of upgrading existing building fabric.
For Nick, his cottage represented an interesting combination of new-build and retrofit. He designed the new-build extension to achieve Passivhaus levels of performance. At the same time, constraints due to the traditional construction and the cottage’s location in a conservation area meant the existing building fabric could not be upgraded to quite the right level to achieve EnerPHit.
Even if full certification to either standard remained just out of reach for Nick’s property, he applied his knowledge and experience to get the best out of both the new and existing building fabric, in terms of energy efficiency and interior comfort. That included finding a solution for hard-to-insulate thermal bridging details.
What thermal bridging solutions
are available for junction details?
A thermal bridge is any discontinuity in a building’s thermal insulation layer. At the junctions between building elements, a thermal bridge is often unavoidable because of structural considerations. Nick found it necessary to detail a solution at the junction of the ground floor with the external wall, and at the base of internal partition walls with their own foundation.
In both areas he specified the PERINSUL HL load-bearing insulation element manufactured by FOAMGLAS®. Being up-to-date on low-energy building solutions, Nick was already aware of the use of PERINSUL HL on projects across Europe. Its availability in the UK made it a viable proposition for his project.
“Putting my ‘builder hat’ on,” said Nick, “knowing the product was readily available made it the best choice.” He also appreciated the relative simplicity of PERINSUL HL, which is made from cellular glass insulation, Nick wanted the peace of mind that comes from a straightforward solution.
PERINSUL HL is stocked by well-known nationwide building supply merchants, and Nick consulted with FOAMGLAS® to check where the product was available. In-keeping with the principles on which the project was designed, he settled on a specialist local stockist: Passivhaus Store (PH Store) in Devon. The advice and service offered by both FOAMGLAS® and PH Store saw the load-bearing insulation units arrive on site in time for the commencement of work.
How does PERINSUL HL achieve better occupant comfort?
At the junction of the ground floor with the external walls - including under sections of rebuilt masonry - PERINSUL HL provided a link between the floor and wall insulation, virtually eliminating the thermal bridge usually caused by the concrete floor slab or below-ground masonry.
And where masonry internal walls sat on their own foundation, PERINSUL HL blocks were coursed in at the level of the ground floor insulation to provide continuity and drastically reduce the flow of heat energy through the wall and into the ground.
Not only did these thermal bridging solutions contribute to the ultra-efficient thermal performance of the building fabric as a whole, they provided better thermal comfort and health benefits for Nick and his family.
The Passivhaus and EnerPHit standards aim to achieve a minimum internal surface temperature of 17 deg.C throughout the whole building. Using PERINSUL HL to insulate thermal bridges removes cold spots on the internal surface, avoiding variations in temperature that cause people to feel discomfort, and preventing a risk of condensation and harmful mould growth.
For more information on PERINSUL HL and how it can benefit your next project small or large, don’t hesitate to contact our team.