Thermal bridging and the performance gap - A case study
PERINSUL HL
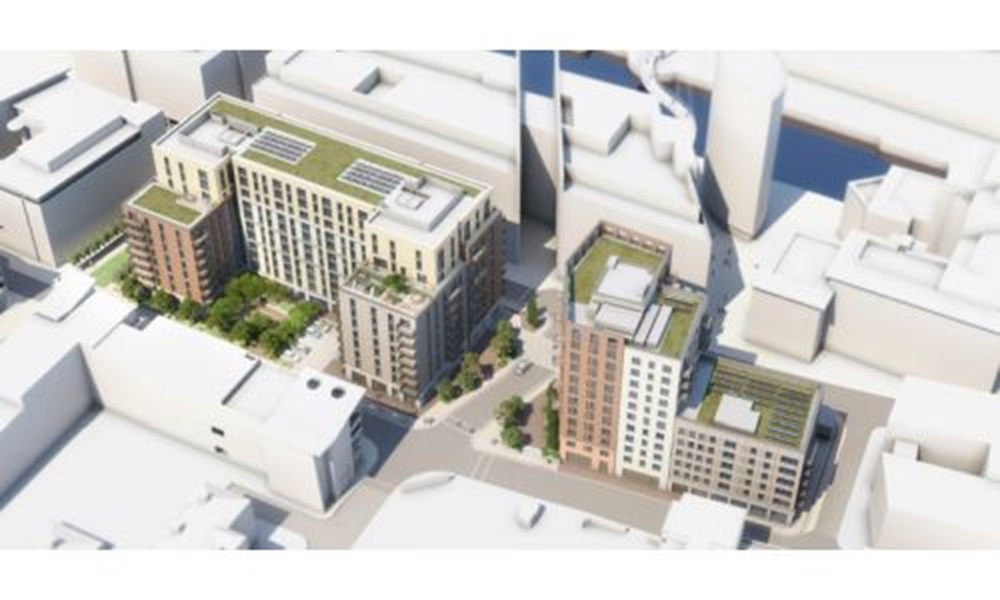
A mixed-use development in the heart of Bristol highlighted how increased awareness of treating hard-to-insulate thermal bridging details can help to improve building performance.
A PERINSUL case study.
It also highlighted the importance of communication throughout the project team to make sure the specified solutions are delivered on site.
It has long been recognised that the energy efficiency predicted for a building at design stage is rarely delivered in the finished product. Once occupied, buildings typically use two or three times more energy than envisaged by compliance calculations - and sometimes a lot more than that. This phenomenon is the performance gap, and eliminating thermal bridges is a key part of reducing it.
What thermal bridging details can benefit
from load-bearing insulation elements?
The project, on Avon Street and close to Temple Mead station, represented a high quality, modern development in Bristol city centre. Similar to other developments of its type, it comprised ground floor commercial premises and several floors of residential accommodation above.
Masonry contractors Millisun Ltd were supplied with drawings by architects Assael Architecture Ltd showing the location of PERINSUL HL load-bearing insulation elements in nearly all of the internal partition walls at ground floor level.
Internal partition walls that break the continuity of the ground floor construction also break the continuity of the thermal insulation in the floor - meaning the wall acts as a thermal bridge, providing a path for unwanted heat loss. Installing PERINSUL HL at the ground floor insulation level achieves continuity of the thermal envelope from one side of the wall to the other, and significantly slows the rate of heat loss through the thermal bridge.
The issue is further complicated in a mixed-use development like Avon Street, because of the variety of rooms and spaces at ground floor level. Heated spaces like the commercial premises themselves, or staff rooms and store areas, are separated from unheated spaces like plant rooms and bin stores. Where the floor meets these separating walls, achieving continuity between the ground floor insulation and the wall insulation is extremely difficult without a product like PERINSUL HL.
The role of the specifier and contractor
in addressing thermal bridging
Detailing thermal bridges to reduce excess heat loss has to be thought about at design stage, so solutions are very much specification-driven. But for those solutions to work, on site teams have to buy into them and understand what is being asked for.
“There aren’t many masonry contractors who have design responsibility,” explained Paul Walmsley, Contracts Manager at Millisun Ltd. “But from a tendering point of view, it’s one of the questions we’ll ask: is there any thermal bridging product in the design?”
For Avon Street, three different sizes of PERINSUL HL were specified. All were 450mm long, with a width to match the width of the masonry wall in which they were installed - 100, 140 or 215mm. The 100mm wide elements were 100mm deep, while the 140 and 215mm wide products were both 140mm deep.
“In a perfect world, everything would be the same depth,” said Paul. Sites are not always that straightforward, however. Sometimes the levels naturally cause a step to occur, or it can be something in the design. And while some designers account for everything in their drawings, others assume such issues will be dealt with on site. Paul’s team split concrete blocks to make up any difference where the 100mm deep PERINSUL HL units met 140mm deep units, ensuring everything was in accordance with the installation guidance.
The role of the manufacturer
in reducing the performance gap
Although the positioning of thermal bridging solutions is governed by what is in the design, when there are queries about the specifics of installation it is good to know that the manufacturer is on hand to offer advice to the contractor.
“Support from FOAMGLAS® was good,” confirmed Paul. “The advice they gave was informative. Sometimes you find yourself in design meetings having to explain things, and it’s great to have that answer as back-up.”
It all starts with creating a product that contractors want to work with, and on that subject Paul was equally enthusiastic about PERINSUL HL: “It’s an easy product to work with, lightweight and fairly readily available. I think our bricklayers would rather build a whole wall in it!”
Providing the right kind of support to designers, specifiers and contractors alike is vital to addressing performance gap issues. There are still too many occasions where a specification is largely cut and pasted from a previous project, so if that project didn’t feature a thermal bridging solution then the next one won’t either.
The good news is that attitudes have shifted in recent years. In the past, thermal bridging solutions might have been excluded on cost grounds. However, the wider benefits in terms of energy efficiency and long term operation costs are much better understood - as is the need to produce designs that can be delivered on site.
About FOAMGLAS® PERINSUL HL
PERINSUL HL is a thermal bridging solution combining thermal performance, compressive strength, durability and dimensional stability in one cellular glass insulation product. It solves the problem of heat loss in hard-to-insulate structural details, improving the energy efficiency of buildings and reducing the risk of condensation and mould growth. It can be used at the base of external walls and internal partitions, below window and door sills, and in parapet details.
For more information on PERINSUL HL and how it can benefit your next project small or large, don’t hesitate to contact our team.